Top Health and Safety Fines of 2022
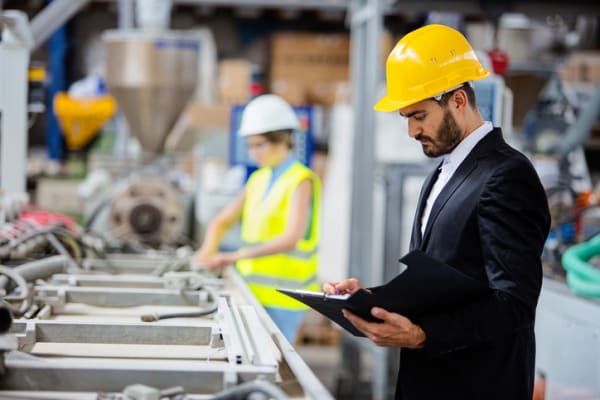
Despite the emphasis placed on proper health and safety practices by legislation and government guidelines, companies still receive significant fines each year due to failings in their health and safety practices. 2022 has been no different in this regard, as we have covered many cases of poor practice leading to fines across a variety of industries. In this post we’ll cover 5 of the most significant fines of 2022 and the failings that led to them.
Operator of UK’s largest oil refinery fined £500,000 following LPG leak
The first case we’ll be discussing is particularly relevant to those studying our IEMA courses or the NEBOSH Environmental Management Certificate. It concerns ExxonMobil, who were fined following the leak of over 15 tonnes of liquid petroleum gas. This is a staggering amount to be released and came as a result of the leak going undetected for 4 hours, ultimately noticed by an off-duty employee about to cycle home. Upon them notifying the company, it took a further hour for the exact location of the leak to be determined and the valve reset to prevent further leaks. Given the volume of LPG released and the significant risk of ignition and explosion it posed, ExxonMobil was served a massive fine of £500,000.
The leak itself was caused by the LPG being sent through pipework at too high a pressure, which the site had no way of detecting despite the need for such a safety system to be in place. This case demonstrates the importance of ensuring the necessary safety systems in place, as well as how one oversight can result in a major incident. It was lucky that, on this occasion, no one was harmed in the incident despite the risk it posed.
Construction company and director sentenced for multiple safety failings.
Our next case, heard at Kilmarnock Sheriff Court, regards three inspections conducted by the HSE, which took place at the construction site at Eglington Park in Irvine between October and December 2016. During these inspections, hazards which posed significant, including unsafe scaffolding, unsafe electrics, inadequate welfare facilities, unsafe traffic management, site tidiness, and a lack of general fire precautions were identified. Follow up inspections intended to assess safety improvements made in response to these identified failings were carried out, though they found no such improvements had been made by the company.
The situation was worsened by the fact that the company director was acting as site manager, which made them directly involved in these failings, a factor which raised the level of sentence and therefore the size of fines due to culpability being higher. This failing is therefore classed as a “deliberate breach or flagrant disregard for the law”. As this occurred with the site manager’s consent, he was therefore negligent and the resulting punishment under this act was attributed, being a of £35,332 fine, as well as 166 hours of community service for the director and the disqualification of him being able to hold a directorship for 2 years.
This case demonstrates that the HSE is not afraid to act against companies and those at senior management positions within them, especially those who ignore significant safety failings across operations. The case is particularly valuable for those studying the NEBOSH Health and Safety Management for Construction Certificate, as it highlights the importance of abiding by notices from the HSE and ensuring safety is prioritised on construction sites.
Firm in court over work at height and welfare issues.
A case was brought to the Blackpool Magistrates’ Court on November 17th, 2020, regarding the company Ruttle Plant (Birmingham) Ltd who were building a new aggregate recycling facility at their site at Common Bank Lane, Chorley. Part of the work included the provision of cladding to the roof, which was carried out using a cherry picker with no edge protection or the suitable safety equipment. The company also failed to have the minimum welfare facilities in place, including hand washing facilities, a factor particularly shocking given this occurred during the Coronavirus pandemic. For the risk it placed employees at and these failings, the company was fined £66,667.
For our students, this is a good case to study in line with the requirements of the NEBOSH General Certificate and NEBOSH Construction Certificate syllabus. It shows the consequences of breaching the CDM Regulation 2015 and Working at Height Regulations 2005, helping to put into context the fines and costs incurred for such breaches. What this case also highlights is the moral reasons for working safely, as in this case it could have, in terms of severity, been fatal or resulted in a major injury. If supervision had been introduced as a control measure (and as required by the Health and Safety at work Act 1974 Section 2(c), these oversights may have been prevented.
It goes almost without saying any work at height should only be carried out by competent workers. When we say competent, this is defined by having the correct skills, knowledge, training, and experience – and of course, don’t forget the right “attitude” towards health and safety. The employer must ensure that these workers are competent. Along with this, as working at height is such a high-risk task, there should be added measures to mitigate the risk to as low as is reasonably practicably through robust planning, monitoring and, of course, risk assessment. For a risk assessment, in this case, the roof was difficult to reach, and workers had to step on to the roof with no edge protection. A thorough risk assessment would have identified these factors, enabling proper control measures and safety mitigation to be put in place. There was also no method statement in place informing employees of the measures that they needed to take or what to do, which, in the absence of any supervision by site management, added to the likelihood of the risk being realised.
Holiday apartments owner fined for serious fire safety breaches
For students studying the NEBOSH Certificate in Fire Safety, the next case we’ll discuss, involving a holiday apartment owner and his company Au Bord De La Mer, may be relevant. They have recently been fined for failing to put suitable fire safety measures in one of their properties, providing an insightful case study. During the incident, which occurred in March 2020, a fire broke out in the apartments, with fire and rescue services needed to save an occupant trapped inside the building. The incident resulted in the company receiving a fine of £12,800, with £10,000 in legal costs on top of this.
Students should recognise the failings concerning the Regulatory Reform (Fire Safety) Order 2005 identified in the following investigation findings. The main failing was found to be that the door into the flat was not fitted with a self-closing device, which allowed the fire to spread rapidly. Other issues found during the investigation were that no records or evidence of proper maintenance of the fire alarm or emergency lighting systems existed; the alarm was also not the correct type and was not switched on. These are all fundamentals for a robust Emergency, Preparedness and Response procedure. Further findings from the investigation were that there was no fire risk assessment in place for the premises, which, as you know from your studies, is a legal requirement under the RRFSO 2005. The lack of a fire risk assessment means that hazards and risks are not identified and cannot be controlled. The most worrying aspect of this is that the “responsible person” had attempted to put in place a company to manage these emergency arrangements; however, due to financial reasons, this did not happen, leaving the occupants, building, and company at risk. These failings to put in place basic control measures and safety procedures could have resulted in far more severe incident, should they have been allowed to continue further.
Sainsbury's fined £1m over 'Booby Trap' which leaves customer with horrific injuries
The last case we’ll discuss was seen by Angela Hayden, CFIOSH, who reported how she was horrified to read of it in IOSH’s Safety Practitioner’s magazine. It related to the horrific injuries suffered by a shopper driving their mobility scooter in the car park of Sainsbury’s Newbury store. Injuries were sustained from strong baler twine which had been used to create a queuing system, after the red and white plastic tape that was used previously had been vandalised. For this purpose, it was pulled taut between two pillars, forming a rigid barrier. A shopper rode into the twine at some speed, face first, and the twine cut into the customer’s mouth, splitting it open, fracturing her teeth, jaw, and palate, which all had to be screwed, titanium plated and rebuilt.
Reading Magistrate’s court was told this unsafe act could have caused a decapitation and had put thousands of customers at risk. The court was informed that there was no risk assessment in place to cover the replacement of the tape with the twine. With the store manager stating to the court that the company “had to rapidly respond to Government guidance to protect the public during a pandemic while continuing to provide an essential service to the public,” but later added, “A sufficient risk assessment would have identified the risks from the baler twine extended between metal posts”. The manager’s decision to use the twine was a response to other health and safety issues that would have arisen from vandalism and weather damage. Nevertheless, it was a decision that was inadequate. This case is an example where control measures are put in place to mitigate one risk but pose a higher risk, with the likelihood and severity of that risk not being considered. Had a thorough risk assessment been conducted due to the change in control measures, this horrific accident could have been prevented.
It is of paramount importance that risk assessments are conducted by “competent” persons, which as we discussed earlier, means these persons should have the skills, knowledge, experience, and training to conduct them to the suitable and sufficient standard required by the Management of Health and Safety at Work Regulations 1999. These should not only be executed by “competent” persons but implemented effectively. Having the relevant risk assessment training is also vital. At Phoenix, we can provide you with the knowledge to assess risks effectively through the NEBOSH National General Certificate.
Incidents such as these could all have been avoided, had proper health and safety protocol been followed. If you want to reduce the risk of such incidents in your workplace, Phoenix can help provide the health and safety training that meets your business’s needs. Contact us to find out more.